Industrial floor grating serves as an essential component in various sectors, from manufacturing plants to commercial kitchens. This versatile flooring solution balances functionality and durability, standing up to harsh environments while ensuring safety and efficiency. Drawing from years of experience and industry expertise, this guide explores why industrial floor grating is indispensable and how it bolsters operational reliability.
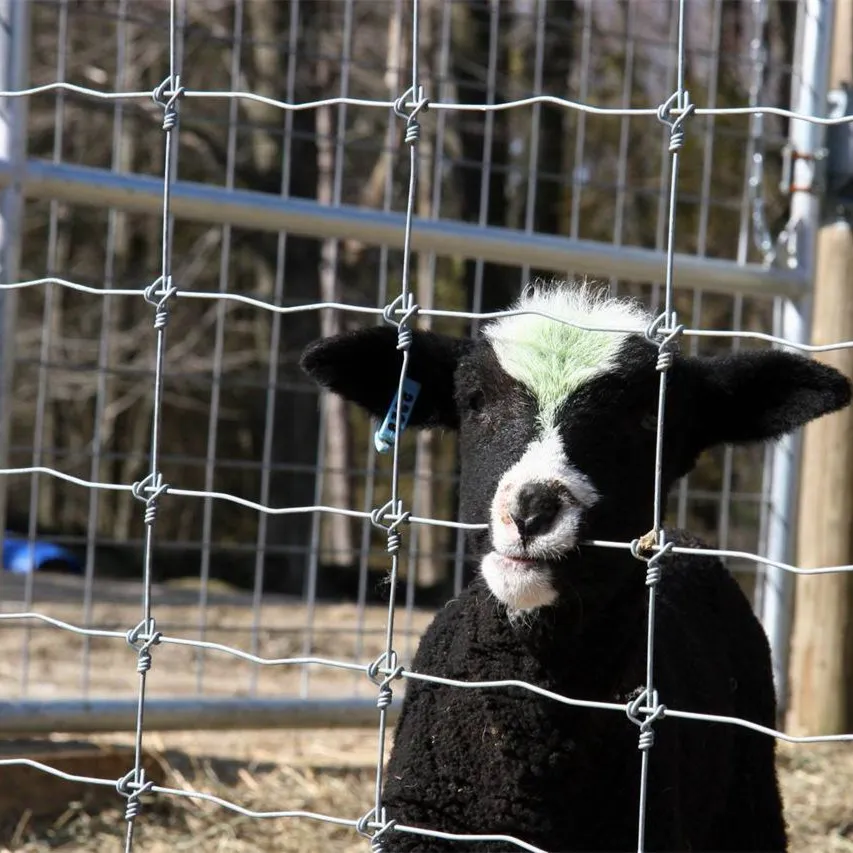
Industrial floor grating is highly praised for its resilience. Crafted to endure heavy weights and continuous pressure, it remains integral to sites where high foot traffic and mechanical wear can degrade other materials quickly. Typically made from steel, aluminum, or fiberglass, each variant offers unique benefits. Steel gratings are synonymous with formidable strength and load-bearing capacity, making them ideal for areas involved in heavy machinery operations. On the other hand, aluminum grating is lightweight yet robust, suitable for installations where weight is a consideration, such as in mezzanine levels that require a balance of strength and load management.
From an environmental perspective, fiberglass grating provides a compelling option. It is resistant to corrosion, making it perfect for chemical plants and places prone to wet conditions. Its non-conductive nature also adds an extra layer of safety, particularly in electrical environments. This characteristic enhances trustworthiness as it minimizes the risk of electrical accidents, prioritizing workforce safety.

Incorporating industrial floor grating translates into improved safety measures. Its open grid design allows for efficient drainage of liquids and debris, mitigating the risk of slips and falls in areas where spills or loose materials are frequent. This feature not only promotes a safer working atmosphere but also ensures hygiene, crucial in food production and processing environments.
industrial floor grating
Industrial floor grating also plays a crucial role in optimizing workflow efficiency. By facilitating easy movement of machinery and personnel, it helps reduce bottlenecks and downtime. In many installations, it supports ventilation requirements by allowing air circulation, which is necessary to maintain machinery and equipment at optimal operating temperatures. This aids in preventing overheating, thus prolonging the lifespan of critical operational assets.
Another aspect enhancing the credibility of industrial floor grating is its ease of installation and maintenance. Prefabricated panels simplify setup procedures, allowing for quick installation and minimal disruption to ongoing operations. Its low maintenance demands further affirm its cost-effectiveness over time. Regular inspections and occasional cleaning can preserve its functional integrity, reducing the need for frequent replacements.
Choosing the right type of grating involves consulting with seasoned professionals who can assess specific site needs. Their expertise ensures the selection of a suitable material and design, tailored to exposure conditions, load requirements, and safety regulations. This informed decision-making process enhances authoritativeness, as it demonstrates knowledge backed by professional practice and compliance with industry standards.
In conclusion, industrial floor grating is more than just a flooring option; it is a strategic component that enhances safety, efficiency, and sustainability. By harnessing expert advice and embracing innovations in material technology, businesses can ensure that their facilities are equipped with the best solutions to support their operations robustly and reliably.